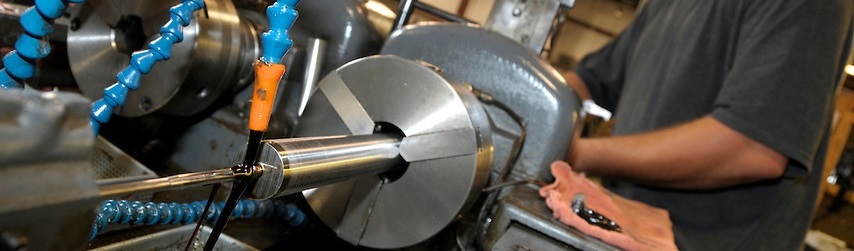

Who we are
Krieger Barrels Manufactures precision single-point cut-rifled barrels in calibers ranging from .20 through 4 Bore for the best target shooters and custom rifle builders in the world. While we do not manufacture complete rifles, we do make barrels for almost any need including competition rifles, high-grade sporting rifles, high-power service rifle competition, AR-10, AR-15, ammunition test barrels and more.
Since John Krieger first began rifling barrels in 1982, our Barrels have been made in America by shooters and for shooters, continuously supporting and advancing shooting sports in America and across the world.
The Steel
There is nothing so important to the making of a good barrel as the steel that a barrel maker uses. Early on we realized we had to give the mill our
own specifications for our steel, accept the higher cost, and then have each lot heat tested as it came in to assure compliance to our strict requirements.
We started by having exhaustive metallurgical tests run on samples of both good and bad steel to determine, on a molecular level, what made good barrel
steel. Having determined this, we met with representatives of the steel mill, the metallurgist, and the heat treater to discuss the results of our findings
and to implement the changes that we needed.
For over 30 years this process has never stopped, and Krieger Barrels continues to test and perfect the steel composition and heat treatment regime. We do not
offer multiple grades of steel. All of our steel must meet the same standards. We do offer most of our barrels in a choice of either stainless steel or chrome
moly. Our stainless and chrome moly barrels are both held to the same standards from initial steel mill quality to final inspection of dimensions and finish.
Single-Point Cut-Rifling
We rifle all of our barrels using the single-point cut-rifling process. Although our machines are state-of-the-art, the process itself is the oldest and slowest method of rifling a barrel. It’s also the most accurate. The cutter removes approximately .0001 inch, or 1 ten-thousandth of an inch, at each pass, thus taking several hundred passes to rifle a barrel. This method produces almost perfect concentricity between bore and groove, a very uniform twist rate, and induces no stress into the steel that later has to be relieved. Along the same lines, we do absolutely no straightening of our barrels as this would only put stress right back into the steel.
Our barrels are lapped after reaming to remove the tool marks, and then hand-lapped again after rifling. It has been said that if a barrel is cut-rifled correctly, it does not have to be finish lapped, and to some extent this is true. It should not have to be lapped to obtain uniformity of dimensions. This should come from the tooling and procedures used. But there is a slight improvement to the finish achieved by finish lapping, and the lay of the finish is now in the direction of the bullet travel so fouling is greatly reduced, and cleaning is made easier. It takes longer to finish lap, but we do it because it makes a better barrel. We are lapping to finishes under 16 micro-inch in the direction of the bullet travel. In contrast the government requires only a 32 micro-inch finish on its M-14 National Match barrels.